Adhesive-free Manufacturing of Continuous Glucose Monitoring Systems
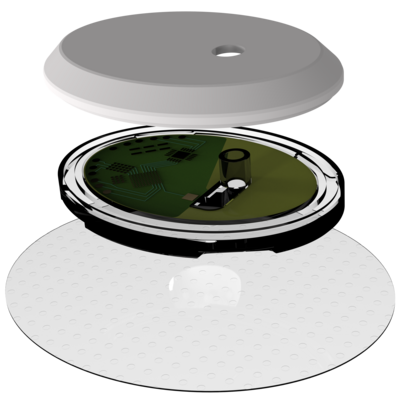
Improve the skin compatibility of your Continuous Glucose Monitoring Systems with an adhesive-free ultrasonic welding process. Without chemicals like IBOA, the comfort for diabetic patients increases while you optimize costs and output of your system at the same time.
Benefit from:
- Clean process without additional joining agents
- Significant cost savings
- Improved comfort and skin compatibility
Learn more about the benefits of ultrasonic welding for your Diabetes Care Device!
Discover Your Diabetes Care Application
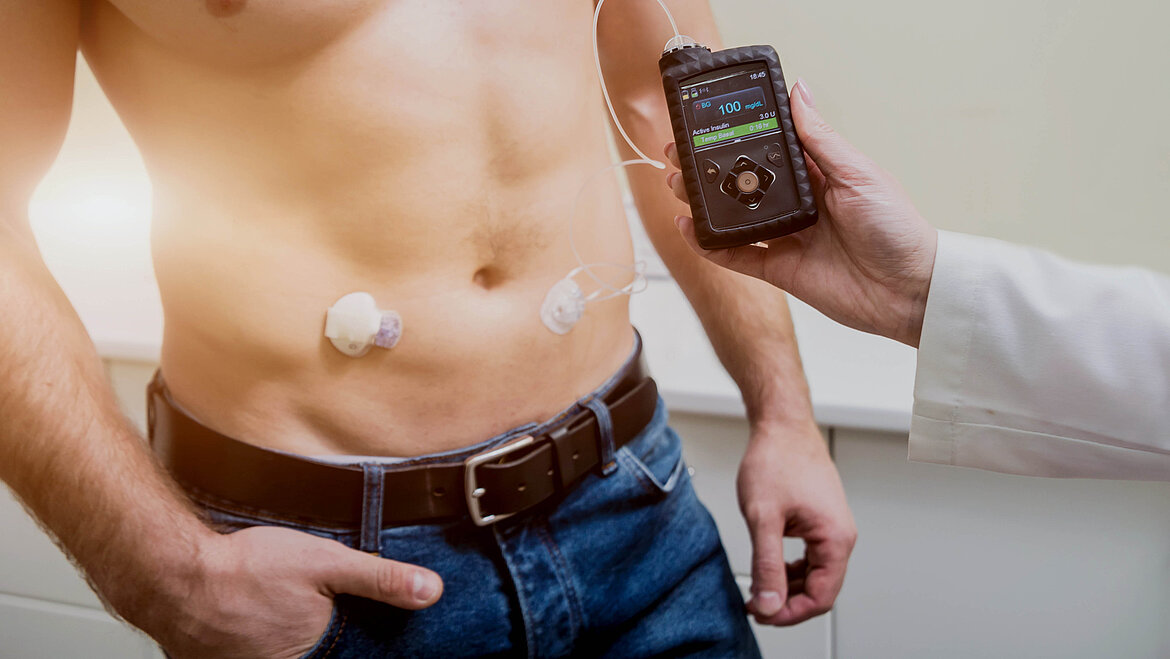
White Paper: Connecting Medical Wearables Safely and IBOA-free
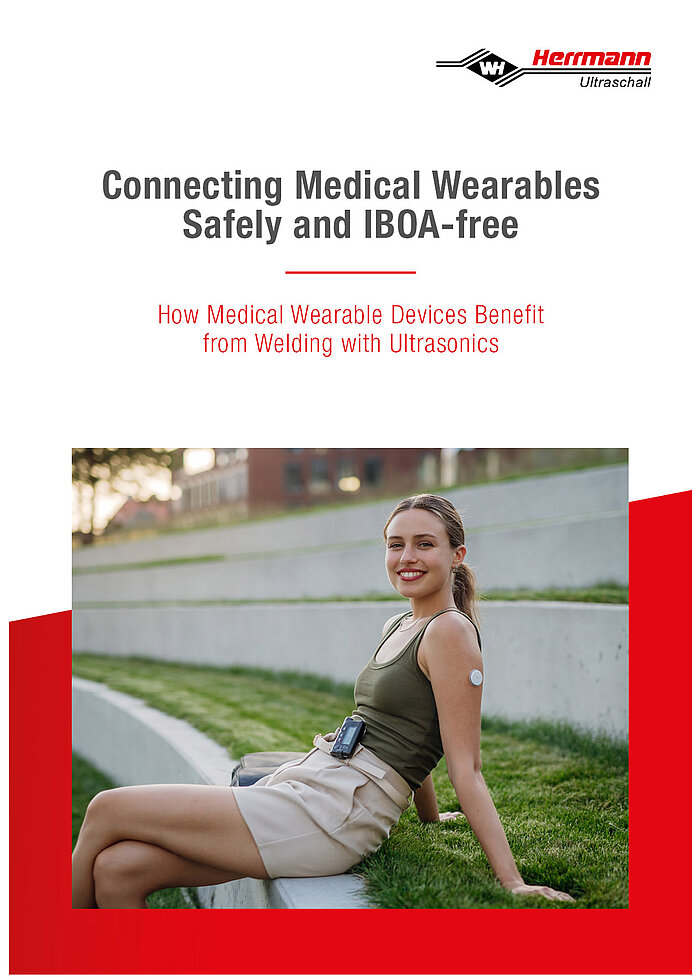
Faster, safer, more efficient: Optimize the manufacturing of your Medical Wearable Device with our ultrasonic technology!
In our free white paper, we show you
✔ The 5 biggest benefits of ultrasonics for CGM systems and other Wearables
✔ How you optimize output, sustainability, and quality control of your manufacturing
✔ Which applications we have already successfully solved
Discover the benefit of ultrasonic welding for your Medical Wearable Device!
Unlock 60+ years of our know-how today
FAQ – The Most Important Questions and Answers about Welding with Ultrasonics
Ultrasonics offers two decisive advantages that increase the comfort and skin compatibility of wearables such as drug delivery devices or CGM systems:
- Improved breathability:
Ultrasonics can be used to create numerous connections within the application without adhesives. This increases the breathability of the application, as fine pores of the membranes are not closed by such joining agents. In addition, an air gap can be created between the band-aid and the component to further increase breathability.
- Removal of harmful chemicals:
Adhesives often contain acrylates such as IBOA. According to studies, these can cause itching or even serious skin irritation in some patients. Ultrasonics can be used to remove such substances from the devices, significantly improving their skin compatibility.
Learn more in our blog post on sustainable and adhesive-free production of medical products.
During ultrasonic welding, heat is only generated for a very short time directly at the contact points of the components that have been defined beforehand. All other areas are only subjected to minimal mechanical stress during the joining process. This protects the components and the devices they contain.
Another important advantage is that the adhesive used to attach the wearables to the skin remains completely intact and is not negatively affected, as is the case with thermal joining processes. This means that the application adheres reliably to the skin and wearing comfort is increased.
You can also find more information on the heat deactivation of adhesives in joining processes in our white paper.
Ultrasonic welding is a safe and reliable solution for manufacturing applications such as insulin pumps or CGM systems.
To achieve this, each welding process is individually developed for your application through test series in the ultrasonic laboratory. This involves defining the right parameters and adjusting the welding tools precisely to the size and properties of the application.
In this way, we ensure that the sensitive components are protected in the best possible way during the welding process so that even delicate elements are connected securely, firmly and with a perfect appearance.
The defined parameters are saved in the generator and exactly reproduced in the production environment by the intelligent controller software in every process, so that safe connections are created even at the highest speeds. Each weld is monitored precisely and documented in the system with up to 150 different welding data values. This enables seamless, digital quality control and therefore maximum safety in the manufacturing of your wearable devices.
Learn more about the gentle ultrasonic welding process in our White Paper:
Ultrasonics can be used for the strong and permanent connection of all common thermoplastic materials, including PP, ABS, PC, etc., with minimal welding times of approx. 80 to 500 milliseconds. This makes the process ideal for manufacturing large quantities.
As no adhesives or other joining agents are required for the connections, there is no need for time-consuming cleaning work, heating up the tools or curing the adhesives, which speeds up the entire joining process.
Thanks to their compact design, ultrasonic welding systems can also be integrated into existing production systems and can precisely monitor even the fastest joining processes.
Find out more in our blog post on automated welding of medical products.
With our Herrmann Engineering, we ensure that we develop the perfect welding solution for your individual application. To achieve this, a project proceeds in five phases:
- Analysis: we want to precisely understand your needs and your requirements for the application. The first step is therefore an intensive exchange about the project and its scope.
- Trusted advisor: We consult you on important questions such as the design of the components and the choice of materials. Together, we will find the right machine solution for you and carry out initial feasibility tests in our ultrasonic laboratories.
- Application engineering: In further welding tests, we define the ideal parameters for the welding process to meet all requirements. We provide you with detailed reports on the laboratory results and recommendations for further steps.
- Perfect product: After the laboratory tests, the results are validated in your production environment. We train your staff in the use of our machines and provide support with integration.
- Global service: After start-up of the welding systems, we are at your side worldwide with our service team. In addition, we offer individual training, spare parts deliveries, maintenance work and many other services to ensure that your manufacturing runs reliably.
Downloads Expert Resources
Learn more about the benefits of our technology for your medical applications. Our downloads contain the knowledge from over 60 years of ultrasonics, providing valuable insights into advanced assembly techniques. By sharing our technical knowledge with you, we ensure a close partnership on equal terms so that we can realize projects as quickly and successfully as possible.
Download our exclusive resources to unlock decades of innovation and stay ahead in the rapidly evolving medical device industry.
Partner with Us
Contact our Medical Team to discover how our premium solutions can elevate the quality and effectiveness of your large-scale manufacturing of medical devices. We look forward to hearing from you!