Welding batteries by ultrasonics
Highest weld quality: process visualization and process stability provide for product safety and repeatability. Small footprint for easy integration into production lines. Ultrasonic metal welding is the ideal solution for maximum quality in production. For our customers, we assume the role of both consultants and application problem solvers with regard to the ultrasonic joining of nonferrous metals.
In addition to leading-technology products, we provide excellent, in-depth application services for solving welding tasks, particularly taking into account the qualitative and economic aspects.
Lithium-ion batteries (LIB)
A typical lithium-ion battery (LIB) uses copper foil as the anode and aluminum as the cathode. The welding of typically 20 to 120 foils to each other requires a high level of joining technology with long time process reliability. Burrs or cracks have to be avoided completely.
As more and more products contain rechargeable lithium-ion batteries (LIB), the battery manufacturers are aiming for ultrasonic welding as reliable battery assembly method. The specifications of the process demand a strong electric contact and no particles on the sealing film of the tab.
Battery management
The development of powerful energy storage systems increases the need for innovative and robust battery systems. State-of-the-art busbars must transmit enormous power. Ultrasonic welding is a highly productive process. Herrmann Ultraschall is able to reproduce a high quality joint under one second cycle time by using high quality and high performance tools and generators (up to 12kW). The connections are characterized by high current carrying capacity and minimal contact resistance with high strength.
Joining aluminum and copper is often a challenge in automation. Ultrasonic metal welding is an excellent solution for permanently bonding the two materials.
Welding battery cells safely and sustainably with ultrasonics
As one of the world's leading developers of customer-specific lithium-ion battery cells, CUSTOMCELLS® pursues the lowest possible reject rate in battery production with maximum process reliability. For the welding of its applications, the development and production company relies on ultrasonic technology in one of their production lines. The ultrasonic welding systems from Herrmann Ultraschall used there minimized the reject rate and optimized production efficiency.
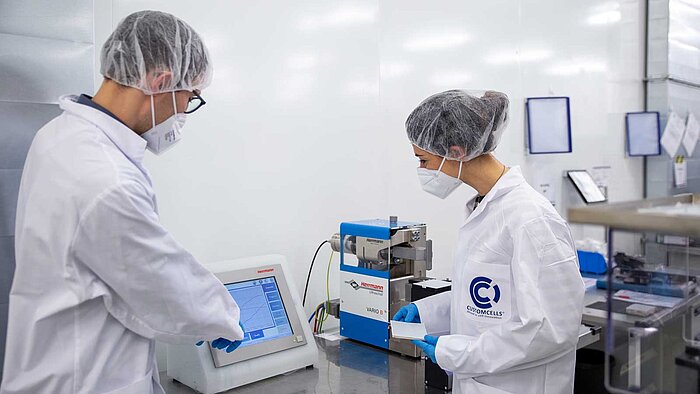