The requirements of components for the electronics industry have become increasingly complex and wide-ranging: Tightness, accurate dimensions, and the impeccable visual appearance of surfaces are typical quality criteria.
Ultrasonic welding allows for cost-effective production and ensures high degrees of production safety and reproducibility of the joining process.
Electrical devices
In addition to housing and display components, it is possible to include electronic components by means of welding or staking. Ultrasonic welding technology allows direct feeding of energy into the joining zone. It’s only possible during the actual welding process and it ensures secure joints of carrier plates and housings. This method avoids putting sensitive electronic parts at risk.
Cable and quick disconnect systems
Male connectors and terminal strips are high-quality safety components and are used in electrical devices, in electronics and in electrical installations. Strong and faultless connections of contacts ensure trouble-free fit and safe current flow. Bonding of contacts by means of ultrasonic technology is a method that allows for connection of different types of materials.
Produce small batches simply faster
For the producers, manually inserting 18 brass female connectors into a plastic frame for a control unit was a laborious and costly process. Ultrasonic welding offered an efficient alternative which considerably shortened the cycle times and was also financially worthwhile – in spite of a low unit count. The versatility of the sonotrode and Herrmann Engineering played a crucial role here.
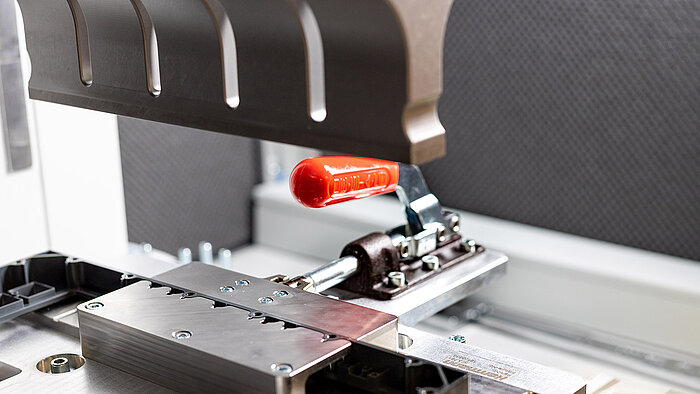